[Anm.:
(falls Sie auf diese Seite direkt durch einen link einer Suchmaschine
gekommen sein sollten),
dies ist ein kostenloser Service von www.sachverstand-gutachten.de
der
Verfasser lädt Sie zum stöbern ein
und freut sich über Rückmeldungen]
download als pdf (Brauindustrie 05_2021)
download als pdf (Getränkeindustrie 08_2021)
Download Tabellenkalkulationsarbeitsblatt KZE-Berechnung [*.xls]
Download Tabellenkalkulationsarbeitsblatt PE-Berechnung [*.xls]
KZE gemäß den allgemein anerkannten Regeln der Technik?
oder
Was darf man ohne qualifizierte Spezifikation erwarten?
Falls nichts anderes vertraglich festgelegt wurde, gelten weder der Stand der Technik [SdT] noch die »billigste noch funktionierende Ausführung« , sondern es gelten gemeinhin die allgemein anerkannten Regeln der Technik [aaRdT] als vereinbart. Aber was bedeutet dies in der Praxis? Darf „mehr“ d.h. nach »höherwertigen Technikfloskeln« geliefert werden? Sind die aaRdT noch zeitgemäß und für einen heutigen und zukünftigen Betrieb ausreichend oder sogar empfehlenswert? Nachfolgend werden einige wichtige Erkenntnisse zur Gestaltung einer Duchlaufpasteurisierung (Kurzzeiterhitzung [KZE]) aufgeführt und kurz diskutiert. Viele der real ausgeführten Anlagen wurden „populistisch“ ausgelegt, d.h. ein hoher prozentualer Wärmerückgewinn wird mit geringstmöglichen Investitionskosten kombiniert, weil der Lieferant behauptet, das sei der Wunsch des Kunden.
aaRdT zeitgemäß?
Die heute gültigen aaRdT entsprachen vor 50 Jahren dem SdT, als z.B. nach dem SdT Festbrennstoffheizungen („Kohleöfen“) in der Bundesrepublik durch „moderne“ Ölöfen oder elektrische Nachtspeicherheizungen ersetzt wurden.
Einige Medikamente sind für den Einsatz am Menschen zugelassen, obwohl sie wegen ihrer erheblichen Nebenwirkungen heute niemals eine Zulassung erlangten. Ein Druckgerät aus Glas, ohne Schutzeinrichtungen und ohne eine entsprechende Überwachung in Verkehr zu bringen, klingt abenteuerlich? Es ist zumindest zweifelhaft, ob man heute (Mehrweg-)Glasflaschen für CO2-haltige Getränke zulassen würde, wenn Glas erst heute erfunden worden wäre. Die Technik der Getränkepasteurisation basiert auf sehr alten Erkenntnissen. Sind diese weiterhin gültig und die technischen Lösungen noch zeitgemäß? Das zu pasteurisierende Getränk und die Menge und Art der Mikroorganismen die inaktiviert werden sollen, sind sicherlich nicht mit den Bedingungen vergleichbar, als die heute noch gebräuchliche Pasteurisationsformel entwickelt wurde. Es gab mehrfach Versuche, die Pasteurisationsformel(n) zu aktualisieren oder zu ersetzen. Insbesondere bei sehr großen Abweichungen von üblichen Heißhaltezeiten und Pasteurisationseinheiten werden erhebliche Fehler wahrscheinlicher. In den nachfolgenden Betrachtungen wird dies jedoch ignoriert werden, da praktisch alle in der Getränkeindustrie installierten und geplanten KZE in einem Bereich betrieben und geregelt werden, der akzeptable Ergebnisse erwarten lässt.
Eine KZE besteht heute üblicherweise aus den Hauptkomponenten: 1. Wärmeübertrager mit 3 Abteilungen (Rekuperation, Erhitzung, Kühlung), 2. Druckerhöhung vor dem Erhitzer, 3. (bei hohen Wärmerückgewinnungen) einem Bypassventil für die Rekuperation für das Anfahren/Reinigen, 4. einem dampfbeheizten Warmwasser-Sekundärkreislauf für den Erhitzer, 5. dem Heißhalter, 6. einem Stellventil zur Aufrechterhaltung des CO2-Sättigungsdrucks, zum Druckabbau und zur Durchflussmengenregelung, 6. Messwertaufnehmer für Durchfluss, Temperatur und Druck, 7. einem Puffertank und 8. einer Schalt- und Steuerungseinrichtung inkl. Protokollierung sowie 10. den Armaturen.
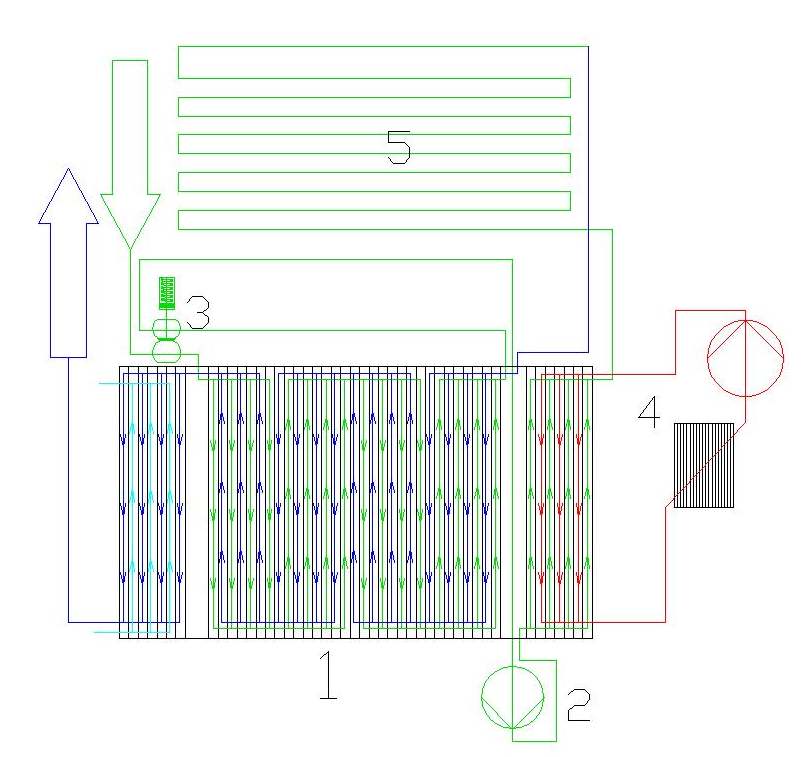
Plattenwärmeübertrager [PWÜ]
Die thermodynamischen, hydraulischen und sonstigen Anforderungen, wie z.B. Reinigungsfähigkeit oder Wartung sind für die drei Abteilungen sehr unterschiedlich. Wenn alle drei Abteilungen in Übereinstimmung mit den aaRdT auf ein Gestell gezwungen werden, dann ist das für mindestens 2 Abteilungen ungünstig. Zeitgemäße PWÜ haben ein festes Spannmaß und damit konstruktiv festgelegte Strömungsverhältnisse und ein konstantes Füllvolumen. PWÜ werden insbesondere bei großen Wärmeübertragungsflächen und bei Rekuperation eingesetzt, da sie hier in der Regel deutlich billiger sind, als Röhrenwärmeübertrager. Die Rekuperation ist immer die größte Abteilung, die auch die Gestell-/Plattengröße bestimmt. Je nach Plattengröße und -geometrie, Prägung der Platten sowie Anzahl und Schaltung der Platten, ergeben sich: die nutzbare Wärmeübertragungsfläche, das Füllvolumen des Wärmeübertragers und der Druckverlust. PWÜ die üblicherweise als Hauptbestandteil einer KZE eingesetzt werden, haben einige systembedingte Nachteile gegenüber (richtig ausgeführten) Röhrenwärmeübertragern: Die Strömungsunterschiede innerhalb einer Platte sind nicht vernachlässigbar, sie werden aber z.B. durch mehrfache Umlenkungen „eingeebnet“. Beim Erhitzer, der häufig eingängig ausgeführt ist, ist davon auszugehen, dass einzelne Bereiche etwas stärker und andere weniger stark erhitzt werden. Platten stützen sich aufeinander ab. Zahlreiche PWÜ weisen Risse in einzelnen Platten auf. Fertigungsfehler sind in der Regel nur durch eine vollständige Demontage zu ermitteln, aber glücklicherweise nicht sehr häufig [Abb.1]. Auslegungsfehler sind dagegen häufiger und bleiben regelmäßig dauerhaft unerkannt.
Abb. 1 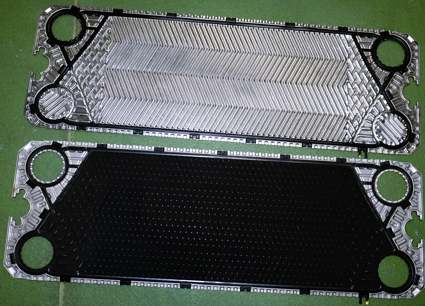
2 falsche Platten wurden nur entdeckt, da sie die halbe Rekuperation blockierten; der Ursprung des schwarzen Belags ist noch unbekannt
Röhrenerhitzer
Für „anspruchsvolle“ Anwendungen sind Röhrenwärmeübertrager gebräuchlich und entsprechen dort auch den aaRdT. Röhrenwärmeübertrager werden (ebenso wie PWÜ) immer mit turbulenter Strömung betrieben. Strömungsgeschwindigkeiten von 2-3m/s werden bevorzugt. Wenn nicht sehr viele Umlenkungen oder extrem lange Wärmeübertrager konstruiert werden, dann müssen die einzelnen Wärmeübertragerröhren einen kleinen Durchmesser von max. ~10mm haben. Verfahrenstechnisch ist ein eingängiger, liegender (5°… 10° geneigter) Röhrenwärmeübertrager besonders vorteilhaft. Statt eines 2 gängigen Röhrenwärmeübertragers können auch 2 eingängige, mit entsprechend optimaler Neigungsrichtung, in Reihe betrieben werden [Abb.2].
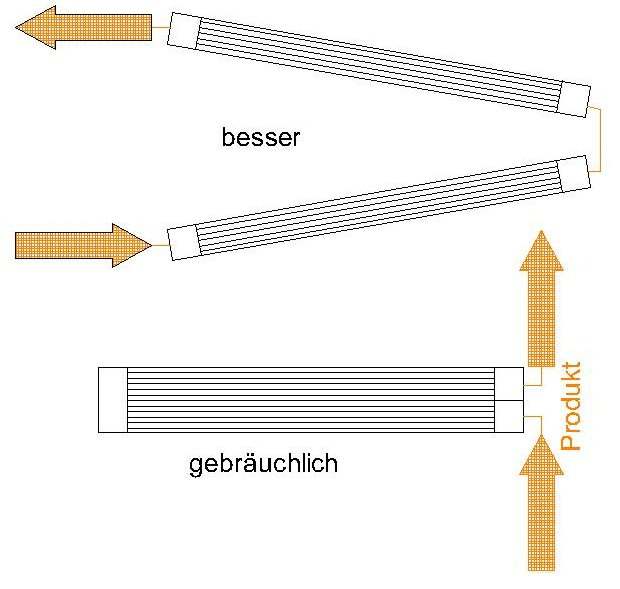
Abb. 2 Einstufige Röhrenwärmeübertrager in Reihe statt mehrstufigen Röhrenwärmeübertrager
Ein besonders kurzer Röhrenwärmeübertrager führt regelmäßig zu geringeren Verpackungs- und Versandkosten und kann evtl. auch einfacher vollautomatisch gefertigt und „ab Lager“ bestellt werden. Für den Anwender bleibt im besten Fall als Vorteil, dass er billiger ist, als ein individuell, optimal ausgelegter Wärmeübertrager. Da im richtig konstruierten Röhrenwärmeübertrager eine leicht nachvollziehbare Strömung herrscht, kann er relativ einfach bei der Berechnung der Heißhaltezeit und somit der Steuerung der Pasteurisationseinheiten integriert werden. Wenn der Produkteintritt direkt in Röhrenrichtung erfolgt, wird die Durchströmung der Röhren ungleichmäßig sein, da durch den dynamischen Druck die Röhren bevorzugt werden, die direkt angeströmt werden [Abb. 3].
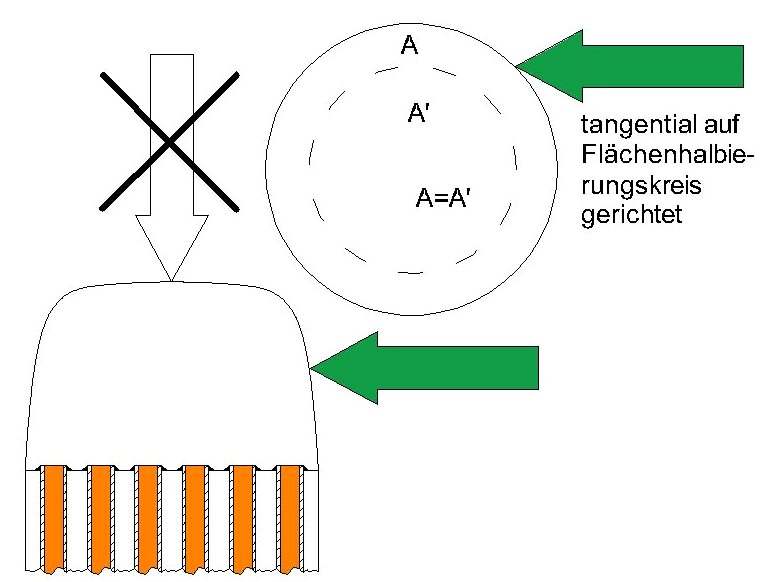
Abb. 3 Produkteintritt in Röhrenwärmeübertrager für gleichmäßige Durchströmung der Röhren
Kühler
Häufig kann ein Kühler ersatzlos entfallen. Falls ein Kühler benötigt wird, sollte er primär aus verfahrenstechnischer und nicht aus Sicht des Lieferanten betrachtet werden.
Heißhalter
Nicht nur weil im als PWÜ ausgeführten Erhitzer Temperaturunterschiede nicht zu vermeiden sind, wird üblicherweise die Pasteurisationswirkung ausschließlich nach der Größe des Heißhalters berechnet. Idealerweise wird der Heißhalter als Rohr mit garantiert turbulenter Strömung ausgeführt. Soll-Heißhaltezeiten von 30 Sekunden bei Nennleistung entsprechen für Bier und zahlreiche Getränke den aaRdT. Zu große Nennweiten des Röhrenheißhalters reduzieren die Fertigungskosten und führen zu sehr niedrigen Strömungsgeschwindigkeiten. Hierdurch kann es zu Ungleichmäßigkeiten während der Heißhaltezeit und somit des Pasteurisationsergebnisses kommen; ebenso wird die Reinigung ungenügend sein. In der Molkerei (mit häufig sehr langen Heißhaltezeiten) ist es gebräuchlich sehr lange Rohre zu verwenden und diese praktisch abstandsfrei aufeinander anzuordnen, um dann das Paket komplett als „Kasten“ zu dämmen. Brauereien und Getränkehersteller bevorzugen große Abstände, um jedes Rohr einzeln reinigen zu können; sie dämmen den Heißhalter häufig nicht und überlassen die konstruktive Gestaltung inkl. der Wahl der Nennweite dem Lieferanten. Obwohl in der Steuerung eine Heißhaltezeit bei Nennleistung von z.B. 30 Sekunden vorausgesetzt wird, ist sie bei den meisten real ausgeführten Anlagen deutlich länger. Die Zu- und Abführleitungen des Heißhalters sind Teil des Heißhalters, auch wenn sie häufig in der Berechnung/Steuerung unberücksichtigt bleiben.
Auslegung
Regelbereiche von 50% (oder 40%) bis 110% der Nennleistung sind häufig anzutreffen. Die Strömungsgeschwindigkeit und der Druckverlust variieren
über entsprechend große Bereiche, was die Auslegung erschwert. Nicht selten wird deshalb nur die Nennleistung berücksichtigt und die Spanne der Betriebszustände wird ignoriert. Teilabschaltbare Heißhalter sind konstruktiv anspruchsvoll, sofern sie nicht durch Koppelbögen „geschaltet“ werden.
Die Pumpe des (Warmwasser-)Sekundärkreislaufs wird häufig so gewählt, dass sie mindestens den doppelten Volumenstrom liefert, der in der Auslegung des Plattenapparates vorgesehen ist, da dies zu einer kleinen mittleren logarithmischen Temperaturdifferenz führt und dadurch die Regelung vereinfacht. Die Pumpenauslegung wird selten nachvollziehbar dokumentiert; durch eine „große Druckreserve“ und einen groß dimensionierten Motor läuft die Pumpe auf der Kennlinie in den vom Abwickler gewünschten Bereich außerhalb der dokumentierten Auslegung.
Die Nenndurchflussmenge, die Temperaturdifferenz der Rekuperation („Wärmerückgewinn“) bei der Nenndurchflussmenge und der maximale Druckverlust werden meist im Lastenheft vorgegeben. In bestimmten Märkten ist es üblich, den Druckverlust (des Kühlabteils) bewusst zur Druckhaltung und zum Druckabbau einzusetzen. Häufig werden auch die Nennheißhaltezeit und die vorgesehenen Pasteurisationseinheiten im Lastenheft aufgeführt.
Wenn bei einer fertigen Auslegung die Fläche verdoppelt wird und alle anderen Parameter idealisiert unverändert bleiben, verdoppeln sich auch der Druckverlust und das Füllvolumen und die Temperaturdifferenz halbiert sich. In der Regel wird man aber versuchen den Druckverlust neben dem Soll-Durchfluss nicht zu verändern; dadurch verändern sich Fläche und Füllvolumen überproportional zur Temperaturdifferenz.
Die Mischzone entspricht etwa 20% des Füllvolumens (inkl. Heißhalter). Eine Vergrößerung der Rekuperation vergrößert die Mischmenge und somit die Kosten beim An-/Abfahren, Produktwechsel sowie bei der Reinigung. Thermische Verluste, die insbesondere durch das Aufheizen und Abkühlen des Edelstahls entstehen, werden durch die Größenänderung der Rekuperation zwar beeinflusst, diese können jedoch bei wirtschaftlichen Betrachtungen zur Vereinfachung außer Acht gelassen werden.
Nachfolgend wird ein Beispiel mit einfachen, typischen Zahlen aufgeführt:
Wenn die Heißhaltezeit im hier aufgeführten Beispiel von 30 Sekunden auf 15 Sekunden halbiert wird, steigt die Pasteurisationstemperatur von 72,35°C auf 74,44°C an und das Volumen in der Rekuperation vergrößert sich um knapp 3% und dass des Heißhalters halbiert sich. In real (auf einem einzigen Gestell) ausgeführten Plattenapparaten werden Erhitzer- und Kühlabteil von hydraulischen und nicht von thermodynamischen Gesichtspunkten bestimmt, sodass diese unverändert bleiben, wenn die Auslegungstemperaturdifferenz der Rekuperation im üblichen Rahmen verändert wird, d.h. die ausgewiesene „Flächenreserve“ wird dadurch vergrößert. Eine Temperaturdifferenz der Rekuperation von 3K ist auslegungstechnisch und von den Investitionskosten her leicht vertretbar. Wenn statt 3K hier 4K gewählt werden, würde der thermische Leistungsbedarf um 11kW (pro 100hl/h) erhöht. Die Rekuperationsabteilung des Plattenapparates würde aber über ein Viertel kleiner. Da die Druckverluste üblicherweise unabhängig von der thermodynamischen Auslegung nahezu konstant bleiben, gibt es bei diesen Änderungen eine Hebelwirkung, d.h. die Auswirkungen der Veränderungen auf Fläche (und Volumen) sind entsprechend größer. In diesem Beispiel müsste die KZE mindestens 2h betrieben werden, um die größeren Verluste, die durch das größere Volumen der Rekuperation bei einer Temperaturdifferenz von 3 K gegenüber 4K entstehen, zu kompensieren.
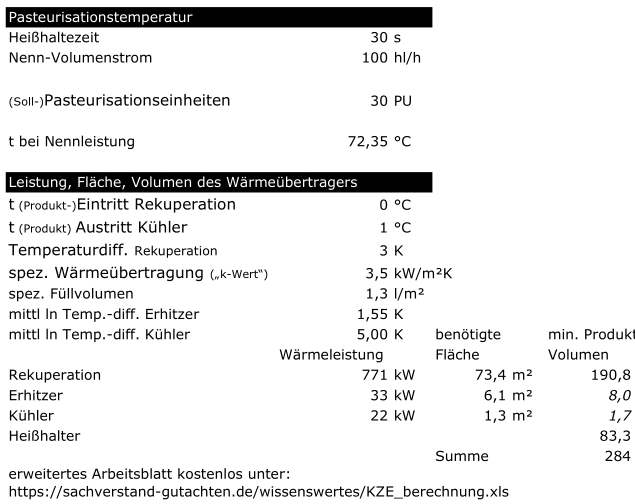
Fazit
Hauptschwachpunkte bei bestehenden Anlagen sind der häufig zu große, schlecht durchströmte ungedämmte Heißhalter sowie Erhitzer und Kühler, die sich mit der Rekuperation das Gestell teilen müssen und deshalb nach hydraulischen statt thermodynamisch-wirtschaftlichen Gesichtspunkten ausgelegt werden. Für die Rekuperation ist der Plattenwärmeübertrager noch immer die kostengünstigste Wahl. Als Erhitzer oder Kühler ist der Plattenwärmeübertrager auf dem Gestell der Rekuperation meist nicht konkurrenzfähig und wird hier aus unbekannten Gründen scheinbar sorglos eingesetzt. Ein mit Dampf direkt beheizter Erhitzer hat eigentlich nur Vorteile, wenn er richtig und groß genug gestaltet wird. Da im Mantel ein Druck deutlich unterhalb des atmosphärischen Drucks herrscht, sind Kondensatabführung und Entlüftung entsprechend anzupassen. Falls ein Kühler benötigt wird, wäre ein NH3-betriebener Röhrenwärmeübertrager die energiegünstigste und wirtschaftlichste Wahl. Der Regelbereich der KZE sollte nicht unnötig groß gewählt werden. Kurze Heißhaltezeiten mit entsprechend höheren Temperaturen bieten Vorteile. Ein Plattenpaket als Heißhalter zu verwenden erfreut primär den Lieferanten des Plattenapparates.
download als pdf (Brauindustrie 05_2021)
download als pdf (Getränkeindustrie 08_2021)
Download Tabellenkalkulationsarbeitsblatt KZE-Berechnung [*.xls]
Download Tabellenkalkulationsarbeitsblatt PE-Berechnung [*.xls]